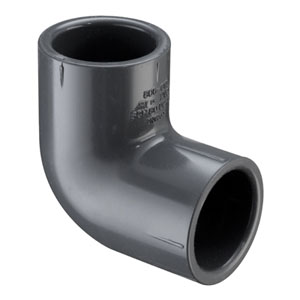
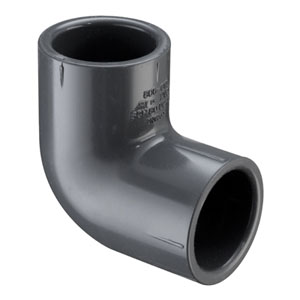
Plastic socket weld fittings are widely used in piping systems that require a strong, leak-free, and corrosion-resistant connection. These fittings are designed for thermoplastic piping systems—most commonly made from materials such as PVC (Polyvinyl Chloride), CPVC (Chlorinated PVC), PP (Polypropylene), or PVDF (Polyvinylidene Fluoride).
They are joined using a solvent welding or heat fusion process, which fuses the pipe and fitting at the socket, creating a permanent bond. While plastic socket weld fittings offer a variety of benefits, especially in corrosive or non-metallic systems, they also have important limitations.
Advantages of Plastic Socket Weld Fittings
- Corrosion and Chemical Resistance
One of the greatest benefits of plastic socket weld fittings is their resistance to corrosion, rust, and chemical attack. Unlike metal, plastics won't degrade when exposed to moisture, acids, alkalis, or saltwater environments.
- Lightweight and Easy to Handle
Plastic fittings are much lighter than their metal counterparts, making them easier to transport, install, and manipulate on the job site, especially in overhead or confined-space installations.
- Smooth Internal Flow
The interior of plastic socket weld fittings is smooth and free of obstructions, resulting in minimal friction loss and more efficient flow in water and chemical systems.
- Leak-Free Joints
Properly installed plastic socket welds form a homogeneous, chemically bonded joint that is leak-proof and durable. Solvent welding effectively fuses the pipe and fitting into a single material unit.
- Cost-Effective
Plastic fittings are generally lower in material and labor cost compared to metal fittings, especially when used in cold water systems, irrigation, or low-pressure industrial applications.
- No Special Tools Required
For PVC/CPVC systems, installation only requires primer, solvent cement, and a pipe cutter—no welding machines or skilled labor are necessary. For heat fusion systems like PP or PVDF, specialized fusion tools are required.
Disadvantages of Plastic Socket Weld Fittings
- Lower Pressure and Temperature Ratings
Plastic socket weld fittings are limited in both pressure and temperature capacity compared to metal systems. For example, standard PVC is only suitable up to ~140°F (60°C), while CPVC extends to ~200°F (93°C).
- Not Suitable for High-Impact or Structural Loads
Plastic fittings can be brittle in cold weather or under mechanical stress. They’re not ideal for environments with significant vibration, impact risk, or structural requirements.
- Requires Cure Time
Solvent cement joints require a curing period before the system can be pressurized. This can delay startup in time-sensitive applications.
- Degradation from UV Exposure
Unprotected plastic piping and fittings can degrade under prolonged UV (sunlight) exposure, making them less ideal for outdoor or above-ground installations unless properly shielded or painted.
- Limited Material Compatibility
Not all plastics are chemically compatible with all fluids. For example, PVC is not suitable for highly concentrated acids or solvents. Proper material selection is critical to avoid premature failure.
- Difficult to Repair or Modify
Once solvent-welded, the joint is permanent and must be cut out and replaced if repairs or changes are needed. There’s no threading or mechanical disassembly possible.
Common Plastic Socket Weld Fitting Materials
PVC (Polyvinyl Chloride) – For cold water and drainage
CPVC (Chlorinated PVC) – For hot water and chemical systems
PP (Polypropylene) – For industrial chemical handling
PVDF (Polyvinylidene Fluoride) – For high-purity or corrosive applications
Typical Applications
Water and wastewater treatment
Pool and spa plumbing
Chemical processing
Irrigation systems
Laboratory and cleanroom piping
Residential and commercial plumbing (cold/hot water)
Final Thoughts
Plastic socket weld fittings offer a practical, affordable, and corrosion-resistant solution for many low- to medium-pressure piping systems. They're especially attractive where chemical compatibility, ease of installation, and system longevity are key concerns. However, their limitations in temperature, pressure, and structural durability must be carefully considered to ensure safe and reliable performance.