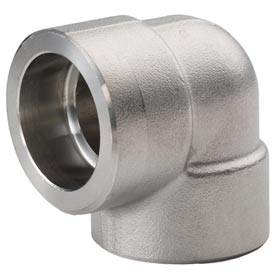
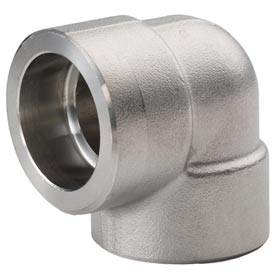
Metal socket weld fittings are a popular choice for high-pressure piping systems in a wide range of industries, including oil & gas, petrochemical, power generation, and water treatment. These fittings are used to create strong, permanent pipe joints by inserting the pipe into a recessed area (or socket) of the fitting, then welding around the outer edge.
Made primarily from forged steel, stainless steel, or other corrosion-resistant alloys, socket weld fittings offer distinct advantages, along with a few limitations. Here's a detailed look at the key pros and cons of using metal socket weld fittings in your next piping system.
Advantages of Metal Socket Weld Fittings
- High Strength and Leak Resistance
Socket weld fittings form strong, durable, and leak-tight joints, making them ideal for high-pressure and high-temperature applications where safety and performance are critical.
- Excellent for Small-Diameter Pipe
They are most commonly used for pipe sizes NPS 2" and below, where butt welding can be difficult or overkill. The recessed socket helps with alignment, making installation easier in tight spaces.
- No Need for Precise Pipe Beveling
Unlike butt weld fittings, socket welds don’t require beveling the pipe ends, which simplifies preparation and reduces labor time.
- Good Flow Characteristics
Socket welds create less turbulence than threaded fittings due to the smooth interior bore, which allows for more efficient fluid flow and less pressure drop.
- Permanent and Tamper-Resistant
Once installed, socket weld systems are tamper-proof, making them well-suited for critical systems where joint integrity is essential over long periods.
- Ideal for High-Integrity Piping Systems
They are widely accepted under ASME B16.11 and are common in Class 3000, 6000, and 9000 pressure ratings, ensuring compliance with stringent industry codes.
Disadvantages of Metal Socket Weld Fittings
- Not Suitable for Larger Pipe Sizes
Socket weld fittings are not available for large-diameter piping. For sizes above NPS 2", butt welding or flanged connections are typically preferred.
- Requires Skilled Welding Labor
Even though beveling isn’t needed, the welding process must still be done by a qualified welder, and inspection may be required for high-integrity systems.
- Potential for Stress Concentration
The geometry of the socket joint can create stress points under cyclic loading or thermal expansion. This makes them less ideal for highly dynamic systems.
- Gaps Can Lead to Corrosion or Cracking
If the expansion gap between the pipe and the fitting is not maintained during welding, it can cause cracking due to thermal stress. Also, the gap can harbor corrosive material if not properly sealed.
- Not Recommended for Hygienic or Slurry Systems
Socket welds create crevices where residue can build up, making them unsuitable for food, pharmaceutical, or slurry applications that require sanitary conditions.
Typical Applications
Socket weld fittings are commonly used in:
Steam and condensate systems
High-pressure fuel or oil lines
Instrumentation and control piping
High-pressure hydraulic and gas systems
Industrial chemical transfer lines
Final Thoughts
Metal socket weld fittings offer a robust, permanent solution for small-diameter, high-pressure pipe systems. They strike a balance between the strength of butt welds and the simplicity of threaded connections. However, they are best used in applications where hygiene isn’t a concern and the pipe size remains small.
Understanding both the benefits and limitations of socket weld fittings ensures you're choosing the right connection type for your system's performance, safety, and longevity.