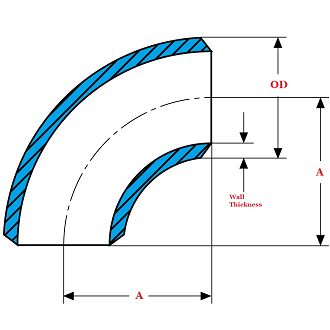
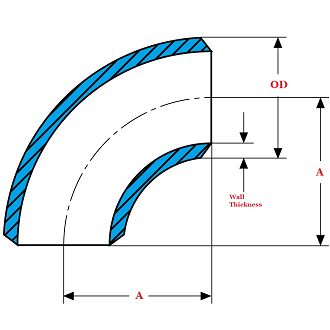
Butt weld pipe fittings are a critical component in piping systems across industries such as oil & gas, chemical processing, power generation, and water treatment. These fittings—used to join pipes and components together via welding at their ends—offer many structural and operational advantages, but they also come with trade-offs.
Below, we’ll explore the key benefits and limitations of butt weld fittings to help you make an informed decision when designing or upgrading a piping system.
Advantages of Butt Weld Pipe Fittings
- Strong, Permanent Connections
Butt welds create a solid, long-lasting joint by fusing pipe and fitting into a single continuous structure. This results in high strength and leak-proof integrity, especially in systems under high pressure or stress.
- Smooth Internal Flow
The inside of a butt-welded joint is flush with the pipe bore, which reduces turbulence, minimizes pressure drops, and prevents material buildup. This is especially beneficial in process piping systems transporting fluids or gases.
- Ideal for High-Pressure & High-Temperature Applications
Because of their strength and durability, butt weld fittings are preferred in environments where extreme conditions—like high temperature, pressure, or corrosive fluids—are common.
- Wide Range of Sizes and Alloys
Butt weld fittings are available in a broad variety of materials (e.g., carbon steel, stainless steel, alloy steel) and schedules (wall thickness), making them adaptable for critical service applications and specialized industry requirements. Above 1” there is no other method with as many available sizes and materials.
- Permanent & Tamper-Resistant
Unlike mechanical connections, welded joints are difficult to alter or disassemble, reducing the chance of tampering or unauthorized changes.
- Reduced Maintenance and Long-Term Reliability
Once installed correctly, butt weld systems require minimal maintenance, making them cost-effective over the long term—especially in hard-to-access locations.
Disadvantages of Butt Weld Pipe Fittings
- Requires Skilled Welding Labor
Installation of butt weld fittings demands highly skilled welders with certifications, particularly for critical service applications. Mistakes in welding can compromise the entire system.
- Time-Consuming Installation
Unlike threaded, press fit or grooved fittings, butt welds require precise alignment, edge preparation (beveling), and weld time, which can extend project schedules.
- Costly Initial Setup
Although the fittings are typically less costly, the combination of skilled labor, welding equipment, and pre-installation inspection (e.g., radiographic testing) can increase upfront costs compared to other joining methods.
- Not Ideal for Temporary or Modular Systems
Because they create permanent joints, butt weld fittings are not suitable for systems that require frequent disassembly, modification, or portability.
- Sensitive to Misalignment and Fit-Up Tolerances
Proper fit-up is critical. Misalignment or poor joint preparation can result in weld defects, reducing strength and flow performance.
- Rigid piping systems often require expansion joints and/or loops.
When to Use Butt Weld Fittings
Choose butt weld pipe fittings when your system requires:
- High integrity under pressure
- Long-term reliability with minimal leaks
- Clean, unobstructed internal flow
- Resistance to high temperatures or aggressive chemicals
- Compliance with ASME B16.9 or B31.3 standards
Final Thoughts
Butt weld fittings remain one of the most trusted and durable options for connecting pipes in critical applications. While they demand higher upfront effort in terms of skill and labor, their benefits in performance, longevity, and system efficiency often outweigh the drawbacks, especially in high-spec industrial projects.