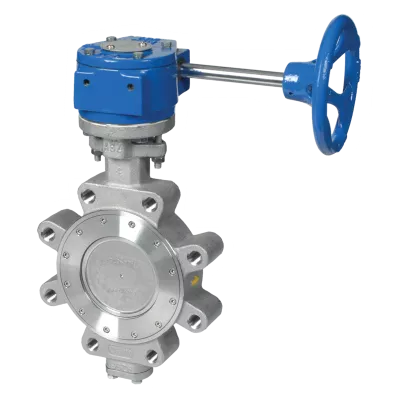
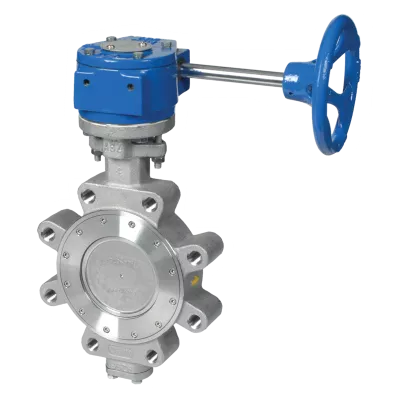
Butterfly valves are a popular choice for isolating and regulating flow in piping systems, thanks to their compact design, lightweight construction, and cost-effectiveness. But not all butterfly valves are created equal. Two major types—resilient seat and high-performance (double offset) butterfly valves—serve very different purposes based on pressure ratings, media compatibility, and operational requirements.
If you're unsure which one fits your application, this guide breaks down the key differences, benefits, and limitations of resilient seated vs high-performance butterfly valves.
What’s the Basic Difference?
Feature |
Resilient Seat Butterfly Valve |
High Performance Butterfly Valve |
Sealing Design |
Rubber/elastomer seat |
Metal or PTFE seat (with offset disc) |
Offset |
Centered disc (zero offset) |
Double offset disc (eccentric) |
Pressure Rating |
Up to 250 PSI (200 PSI is standard) |
Up to 600 PSI or more |
Temperature Range |
Up to ~200°F (elastomer-dependent) |
Up to 900°F (depending on materials) |
Applications |
Low-pressure water, air, and non-corrosive fluids |
Steam, gas, hydrocarbons, and higher-pressure services |
Resilient Seat Butterfly Valves (RSBV)
Also known as rubber-seated butterfly valves, these valves feature a centrally mounted disc that compresses against a soft seat (often EPDM, Buna-N, or Viton) to form a seal.
✔ Pros:
- Cost-Effective – Lower material and production costs
- Simple Operation – Ideal for manual or low-torque actuation
- Tight Shutoff – Excellent bubble-tight seal in low-pressure systems
- Corrosion Resistant – Non-metallic seat resists water and many chemicals
- Low Maintenance – Minimal moving parts, fewer failure points
✖ Cons:
- Limited Temperature and Pressure – Typically up to ~200°F and 150–250 PSI
- Seat Wear – Soft seat can wear faster in abrasive or high-cycling applications
- Not Suitable for Critical Applications – Not Fire-Safe or API-rated
Common Uses:
- Water distribution and treatment
- HVAC and chilled water systems
- Food-grade systems (with FDA elastomers)
- Low-pressure air, gas, and chemical systems
High Performance Butterfly Valves (HPBV)
These valves use a double-offset disc design, where the disc is offset from the centerline of the pipe and shaft. This design reduces seat contact during operation, reducing wear and allowing higher pressure and temperature ratings.
✔ Pros:
- High Pressure Capability – Often rated for up to 600 PSI and beyond
- Higher Temperature Tolerance – Handles steam, hydrocarbons, and hot gases
- Fire-Safe & API-Compliant – Many HPBVs meet API 609 and other standards
- Tight Shutoff with Longer Life – Less seat deformation over time
- Versatile Seating Options – Soft seat, metal seat, or PTFE seat for chemical resistance
✖ Cons:
- More Expensive – Higher material cost and machining complexity
- Higher Torque Requirement – May need gear or powered actuators
- Requires Precise Installation – Misalignment can affect sealing performance
Common Uses:
- Oil & gas, petrochemical, and refinery systems
- Power plants and steam lines
- Marine and offshore platforms
- Industrial air, vacuum, and high-cycle process systems
When to Choose Each Type
Application |
Best Choice |
HVAC and chilled water |
Resilient Seat |
Clean water or irrigation |
Resilient Seat |
Steam or hot oil lines |
High Performance |
Chemical processing |
Depends on media—likely HPBV with PTFE seat |
Gas pipelines |
High Performance |
Budget-conscious, low-pressure applications |
Resilient Seat |
High-pressure or fire-safe applications |
High Performance |
Final Thoughts
Both resilient seat and high-performance butterfly valves are invaluable tools in flow control, but they serve very different needs.
- Choose a resilient seat butterfly valve when you need an affordable, low-pressure solution for water or general utility service.
- Opt for a high-performance butterfly valve when your system demands higher pressure, temperature, and reliability under severe conditions.
The right valve can enhance your system’s safety, efficiency, and longevity. Always consult pressure/temperature charts and media compatibility before making a selection.