Flange Face Types Explained: Raised Face, Flat Face, and Ring Type Joint
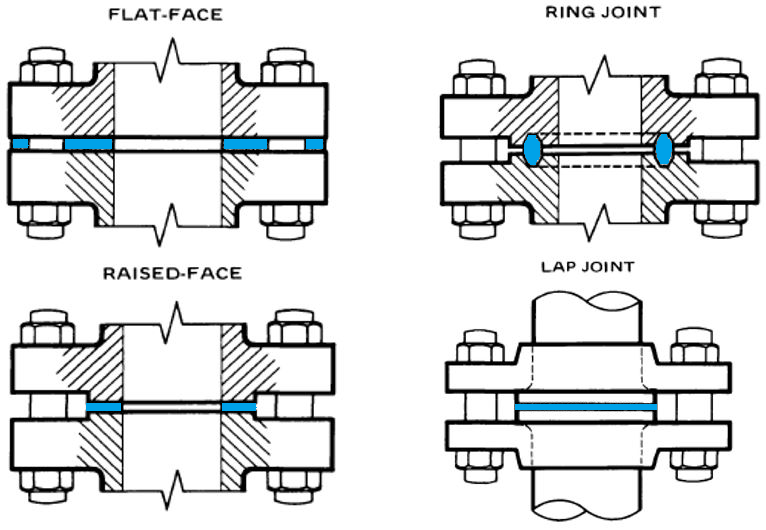
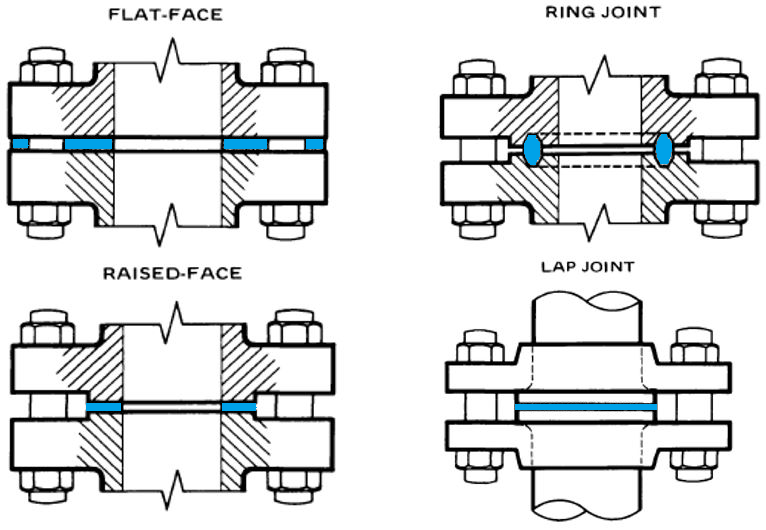
When designing or maintaining a piping system, it’s not just about choosing the right flange material and pressure class; flange face type is just as important. The face of a flange determines how it seals against its mating surface, how it distributes pressure, and which gasket types it can use.
In this guide, we’ll break down the three most common flange face types: Raised Face (RF), Flat Face (FF), and Ring Type Joint (RTJ) — including where they’re used, how they perform, and what to consider when specifying them.
Raised Face (RF) Flanges
The most common flange face type in process piping.
What Is It?
A Raised Face flange has a small circular surface that protrudes slightly from the flange body, typically 1/16" (Class 150–300) or 1/4" (Class 400–2500). The gasket seats on this raised section rather than the full flange face.
Where It's Used
- Industrial and commercial piping systems
- Refineries, power plants, chemical processing
- Systems with standard pressure and temperature ranges
Gasket Compatibility
- Spiral wound gaskets
- Ring gaskets
- Full-face gaskets
Advantages
- Provides greater sealing pressure in the gasket area
- Compatible with a wide variety of gasket types
- Easy to identify and widely available
Considerations
- Not ideal when connected to cast iron flat face flanges, valves, and pumps (can cause stress and cracks)
Flat Face (FF) Flanges
Used primarily in lower-pressure, less demanding applications.
What Is It?
A Flat Face flange has a smooth, flat sealing surface that runs flush across the flange face. The entire face is in contact with the gasket, usually requiring a full-face gasket.
Where It's Used
- PVC and fiberglass piping systems
- Low-pressure water and air lines
- Pump and equipment connections using cast iron
Gasket Compatibility
- Full-face gaskets only
Advantages
- Provides full contact with flat-faced mating flanges (e.g., cast iron)
- Prevents overstressing brittle materials
- Simpler machining = lower cost
Considerations
- Less sealing pressure than RF
- Not suitable for high-temp or high-pressure systems
- Requires perfectly aligned, full-face gaskets
Ring Type Joint (RTJ) Flanges
Engineered for high-pressure, high-temperature, and critical sealing conditions.
What Is It?
An RTJ flange has a precision-machined groove in its face, designed to accept a metal ring gasket. When bolted together, the ring deforms to create a metal-to-metal seal under extreme conditions.
Where It's Used
- Oil & gas, petrochemical, and offshore platforms
- High-pressure steam systems
- ANSI 300# and higher pressure classes
Gasket Compatibility
- Octagonal or oval metal ring gaskets (R-style or BX-style)
Advantages
- Ultra-reliable seal in extreme pressure and temperature
- Resistant to blowout or fire damage
- Ideal for critical service where leaks are unacceptable
Considerations
- More expensive than RF or FF
- Requires precise alignment and installation
- Not reusable — metal ring gaskets deform permanently
Key Takeaways
Face Type |
Best For |
Seal Style |
Pressure Range |
Raised Face (RF) |
Standard industrial use |
Gasket compression on the raised area |
150–2500 Class |
Flat Face (FF) |
Cast iron, PVC, low-pressure |
Full-face gasket |
125–300 Class |
Ring Type Joint (RTJ) |
High-pressure/high-temp critical systems |
Metal ring in machined groove |
300 Class and up |
Choosing the Right Flange Face
When specifying a flange face, consider:
- Pressure rating and temperature range
- Mating material (e.g., steel-to-cast iron = FF)
- Gasket type and compatibility
- Application criticality — is leakage acceptable?
Need Help Selecting the Right Flange?
At Hayward Pipe & Supply Co., we stock a wide range of ANSI B16.5 flanges in carbon steel, stainless, and alloy materials — available in RF, FF, and RTJ face types. Whether you’re designing a new system or replacing an old flange, our team is here to help.