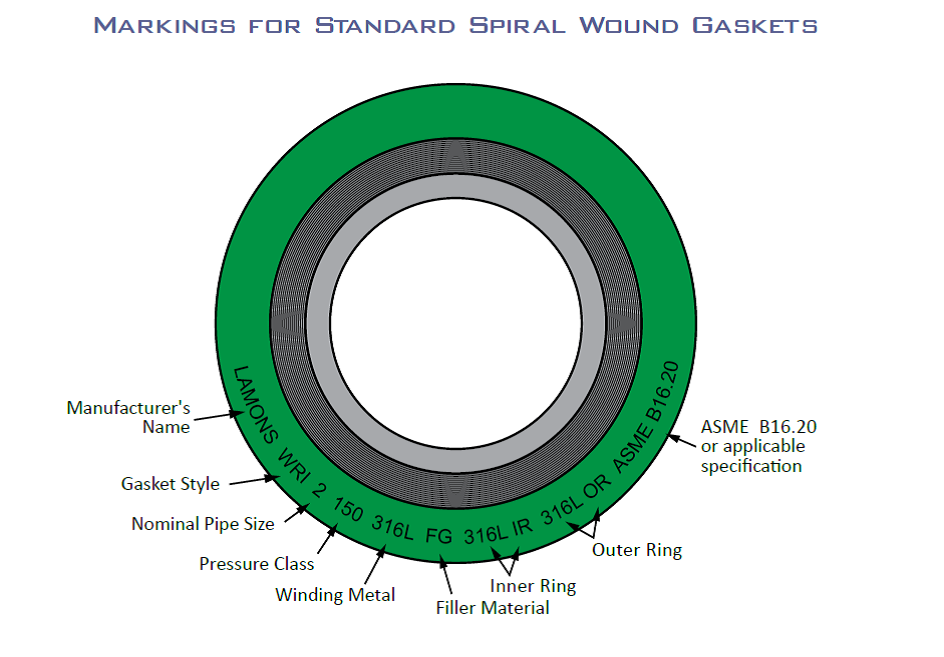
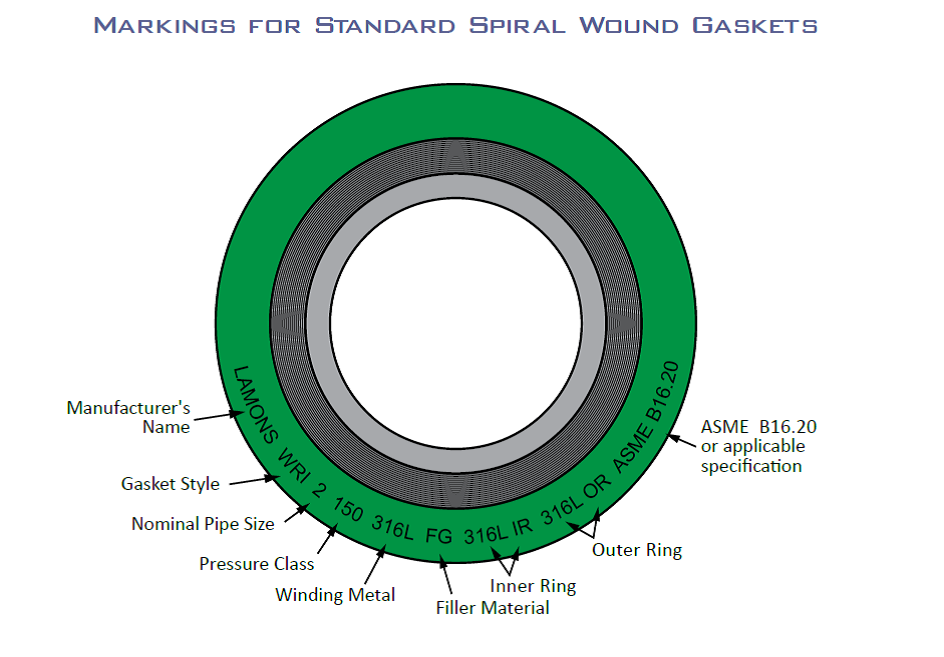
In any flanged piping system, the strength of the connection is only as good as the weakest link and that’s often the gasket or bolting. Whether you’re assembling a steam line, a chemical system, or a water distribution header, understanding how gaskets and bolts work together is critical to achieving a tight, long-lasting seal.
This is an overview of flange gasket types, bolting methods, and installation best practices to help you minimize leaks and maximize system integrity.
Why Gaskets and Bolts Matter
Flanged joints are designed to mechanically compress a gasket between two faces. The bolt torque must be high enough to create sufficient gasket stress, but not so high that it damages the gasket or distorts the flange.
A poorly selected or improperly installed gasket or bolt can lead to:
- Leaks under pressure
- Fugitive emissions
- Premature gasket failure
- Costly downtime or repairs
Types of Flange Gaskets
The right gasket depends on the flange type, media, temperature, and pressure. Here are the most common types:
- Full-Face Gaskets
- Covers the entire flange face with bolt holes
- Used with Flat Face (FF) flanges
- Common in low-pressure water, HVAC, or cast iron systems
- Raised Face Gaskets (Ring Gaskets)
- Fits inside the bolt circle on Raised Face (RF) flanges
- Available in various materials (compressed fiber, PTFE, graphite)
- Used in most industrial process systems
- Spiral Wound Gaskets
- Made from metal windings and filler (graphite, PTFE)
- Handles high pressure and temperature fluctuations
- Excellent for steam, chemical, and refinery applications
- Ring Type Joint (RTJ) Gaskets
- Precision-machined metal rings used with RTJ flanges
- Forms a metal-to-metal seal
- Ideal for high-pressure, high-temperature environments (300# and up)
Bolting Basics: What You Need to Know
Correct bolting is just as important as gasket selection. Flange bolts create the clamping force that compresses the gasket. Key factors include:
- Bolt Material
Choose bolt or stud material based on service conditions. Common options:
- B7 (Alloy Steel): For high strength and elevated temperatures
- Stainless Steel: For corrosion resistance
- Zinc-Plated or Galvanized: For general service and outdoor use
- Bolt Torque
Proper torque ensures even gasket compression. Over-torqueing can crush gaskets or warp flanges. Under-torqueing leads to leaks.
- Lubrication
Anti-seize or thread lubricant ensures consistent torque and prevents galling on stainless fasteners.
- Bolt Patterns
Always use a cross-pattern sequence to apply torque evenly:
- Hand-tighten all bolts
- Torque to 30%, 60%, then 100% in a star pattern
- Finish with a circular torque pass
Common Mistakes to Avoid
- Mixing gasket types with the wrong flange face (e.g., using ring gaskets on flat face flanges)
- Reusing gaskets — always use a new gasket when breaking a connection
- Dry bolt installation — this often leads to uneven torque and failure
- Ignoring environmental or chemical compatibility when selecting gasket material
Pro Tips for a Leak-Free Seal
- Use calibrated torque tools (not just a wrench and guesswork)
- Check flange surfaces for pitting or warping
- Align flanges properly before torqueing
- Use washers to distribute bolt load evenly
Final Thoughts
A flange connection may look simple, but achieving a reliable, leak-free seal takes thoughtful selection of gaskets and bolts, proper torqueing techniques, and attention to detail. Whether it’s steam, air, chemicals, or water; every system benefits from well-executed flange assembly.
Need Help Sourcing the Right Gaskets and Bolting?
At Hayward Pipe & Supply Co., we carry a wide selection of:
- Spiral wound and full-face gaskets
- Metal ring joint gaskets
- Bolt kits and stud sets
- ASME and ANSI flanges in all materials